With Over 40 Years Experience!
Meet Our Founder Giuseppe Alleva
Giuseppe has been working in this industry since 1982! His experience began in Computer and Printer supplies back when there was 8″ floppy discs and printer ribbons! He has worked for manufacturers and distributors, and one of the largest Computer Product companies his entire career! The experience you get is from someone who has experienced the entire growth of the computer and network world! Our mission is to offer that experience to you. We are the only source you need for anything in your environment.

Director of New Relationships
Kara Barrett
Kara came to Innovative IT Products with a decade of experience in customer service. We knew right away that she should be the person who introduces Innovative IT Products to new clients.
You only get one chance for a first impression, and we are glad Kara has that role!

Innovative IT Products has been in the business of providing IT solutions since 1982 and has been working with Independent Dealers, Distributors and Resellers to grow their Imaging Supply Programs. We offer a large variety of products including, HP, Brother, Canon, Dell, Lexmark, and IBM. Innovative IT Products has an extensive line of color, jumbo, and micro cartridges. We are an industry leader with a strong reputation for quality and service.
Innovative IT Products has always made quality our number one focus. Selling high performance, reliable products allows our customers to succeed. And when you succeed, we succeed. Our products are post tested prior to leaving our facility to ensure that they are free of defects in materials and craftsmanship. This allows us to have some of the best trained and knowledgeable technicians in the industry.
Innovative IT Products is equipped to handle all size customers and meet your packaging needs. We utilize private labeling or custom packaging based on your needs or requirements.
Program Highlights
We offer a large variety of products including, HP, Brother, Canon, Dell, Lexmark, and IBM. Innovative IT Products has an extensive line of color, jumbo, and micr cartridges. We are an industry leader with a strong reputation for quality and service.
Our dedication to being the only source you need for all of the needs in your environment is second to none!
Innovative IT Products has always made quality our number one focus. Selling high performance, reliable products allows our customers to succeed. And when you succeed, we succeed. Our products are post tested prior to leaving our facility to ensure that they are free of defects in materials and craftsmanship. This allows us to have some of the best trained and knowledgeable technicians in the industry.
- 100% No Hassle Warranty
- American Made Products
- American Distribution Channels
- 100% TAA Compliant Product Line
- Same Day Shipping Capabilities
- 40 Years Experience
- Wide Range of Products
- The Only Source You Need
- FREE Tech Support
- National Recycling Program
- Dedicated Account Reps
- Anything You Need, We'll Find it For you
Technical Support
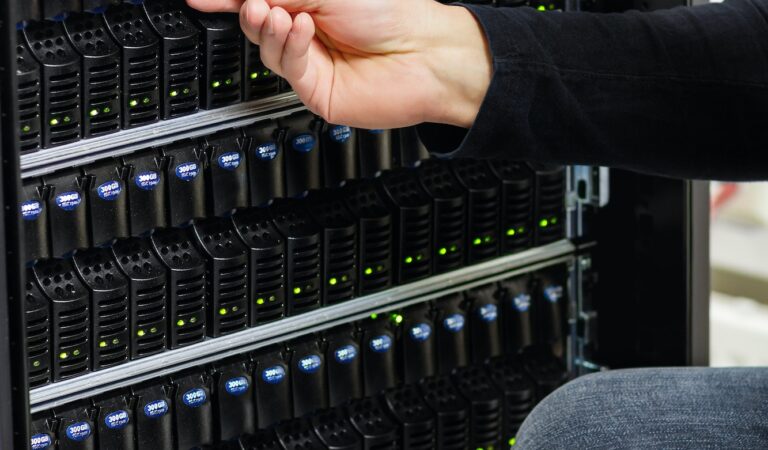
Innovative IT Products offers a free technical support line. The immediate availability of experienced Customer Care Representatives and Technical Support Specialists allow us to potentially solve many issues over the phone. With complete customer satisfaction as our main goal, you have our word that Innovative will investigate the situation thoroughly. When a call comes in it is evaluated and then forwarded to the correct specialist trained in that particular area. All calls are answered and not transferred to a voice mail. Whether it is sending a replacement out immediately or talking them through pulling a seal, by using our support line the end result is a faster solution for your customer.
Our Technical Support Team looks forward to working with you.
CALL US TODAY: 877.515.6766
USA Manufacturing Process
Core Inspection Department
Innovative IT’s Manufacturing process is based on the utilization of Virgin Cores. Prior to arriving at the Set Up department, Core Specialists complete 100% inspection of each individual cartridge to insure that the Set up department is receiving a quality product that is free of broken or defective outer components.


Setup Department
Each setup follows a stringent procedure. The person or personnel responsible for the set up before being released to the Manufacturing/Production Department must complete a detailed Job Sheet/Routing Sheet listing manufacture of components (Drums, Pcrs, Magrollers, Wiper blades, Doctorblades, Chips etc) and lot Id numbers (For tractability) being used for that particular setup. All components percentages have been pre determined through stringent.
Research and Development procedures following the STMC and ASTM guidelines for testing all in one-laser cartridges to determine best combinations of new aftermarket and durable non-wearing oem components to achieve page yield print density and over all consistency equal or greater to the oem product.
Manufacturing
Innovative IT toner cartridges are manufactured in a single cell system. Technicians have no less than three years experience in cartridge manufacturing. Before any job is started, the technician must review the Job/Routing Sheet and do a physical inspection to verify that all correct components and toner match the routing sheet and sign off on the documentation. Technicians are responsible for the inspection of new aftermarket and durable non-wearing OEM components utilized. Once the cartridges are completed the technician places proper labeling and a bar code on each individual cartridge the bar code has various information that list the date of manufacturing ID number of the technician etc before inspection by Quality Assurance Department.


Quality Assurance Department
Quality Assurance personnel are responsible for the testing and visual inspection of all cartridges manufactured before being released to the packaging department. Quality Assurance personnel testing procedure includes the use of a Toner Head Print Test Messager (Approved testing equipment by the ITC Council). The Toner Head runs a series of a four-page configuration test pages. Blank Page (Identify any type of drum and pcr defects) Lombardi Page (Graphics and density readings) Gray Scale Page (Identify any type of contact or component defects) Black Page (Identifying all component defects). After a visual inspection of each test copy and no imperfections are detected the Quality Assurance personnel then places a color-coded label on the cartridge and a copy of the approved test print is placed with the toner cartridge. The packaging department will perform a final visual inspection.
NOTE* Quality Assurance Department also performs a random ten percent inspection of stock inventory to insure that all department procedures have been followed.
Packaging Department
Packaging personnel are responsible for the proper packaging of cartridges to insure that a quality product arrives to our customers Before the cartridge is packaged the packaging personnel performs a final visual inspection to check for proper labeling and cleanliness of the cartridge. Packagers are required to review the purchase order to verify that the proper packaging materials and labeling meet customer specifications once verified the packager must also include the copy of the cartridge test print that was approved by the Quality Assurance Department.

Success Rate Statement
Innovative IT Products has always made quality our number one focus. Providing a quality and reliable cartridge, that outperforms the other remanufactured brands, has given us a great reputation throughout the industry for the reliability of our toner cartridges. There are several steps that we take to ensure the greatest quality possible.
We only use original OEM cores that haven’t been previously remanufactured. This ensures the integrity of the core and guarantees that the core has never been altered or manipulated in any way.
Once the OEM core has been disassembled, we replace all of the internal components with only the best aftermarket components available. These components have been qualified through extensive testing by our research and development department.
Every toner cartridge is post tested prior to leaving our facility to ensure that they are free of defects in material and workmanship. Our production is set up different than most other toner remanufacture facilities. Instead of using a production line where each technician is only responsible for one step of the cartridge, each technician builds the cartridge from start to finish and is 100% responsible for each cartridge that they build. This has allowed us to have some of the best trained and knowledgeable technicians in the industry.
Every toner cartridge that leaves our facility has a barcode placed on it which gives us the ability to track the lot number for each internal component used, the technician it was built by and the date it was built on. This allows us to track a defect back to a particular builder and component and gives us the data needed to continually improve our quality.